How tight should I screw my thru-axles?
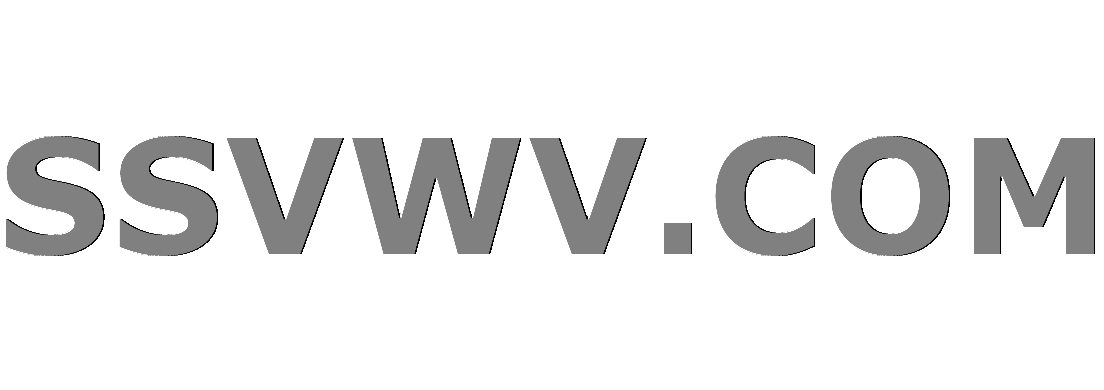
Multi tool use
I have a new road bike with thru axle and disc brakes (Ultegra). I noticed that depending on the how tight I screw the axle in the frame, the brake disc will be closer to either side of the brake pads. I didn't pay attention at first, so now the rear left pad is much more worn that the right one.
Is there a way to find the perfect torque to make sure that the disc is perfectly centered?
disc-brake hydraulic-disc-brake thru-axle
add a comment |
I have a new road bike with thru axle and disc brakes (Ultegra). I noticed that depending on the how tight I screw the axle in the frame, the brake disc will be closer to either side of the brake pads. I didn't pay attention at first, so now the rear left pad is much more worn that the right one.
Is there a way to find the perfect torque to make sure that the disc is perfectly centered?
disc-brake hydraulic-disc-brake thru-axle
Do your axles have recommended torque values printed on? I'd also contact the shop that sold your bike about torque affecting the alignment, that's not supposed to happen and might be a warranty/service case.
– Klaster_1
Jan 4 at 16:36
1
I don’t think they are mentioned, anyway, the axles come with a handle to easily remove a wheel on the side of the road, i couldn’t check the exact torque if I have a puncture during a ride.
– Rwanou
Jan 4 at 21:35
add a comment |
I have a new road bike with thru axle and disc brakes (Ultegra). I noticed that depending on the how tight I screw the axle in the frame, the brake disc will be closer to either side of the brake pads. I didn't pay attention at first, so now the rear left pad is much more worn that the right one.
Is there a way to find the perfect torque to make sure that the disc is perfectly centered?
disc-brake hydraulic-disc-brake thru-axle
I have a new road bike with thru axle and disc brakes (Ultegra). I noticed that depending on the how tight I screw the axle in the frame, the brake disc will be closer to either side of the brake pads. I didn't pay attention at first, so now the rear left pad is much more worn that the right one.
Is there a way to find the perfect torque to make sure that the disc is perfectly centered?
disc-brake hydraulic-disc-brake thru-axle
disc-brake hydraulic-disc-brake thru-axle
edited Jan 4 at 20:58


Argenti Apparatus
33.2k23583
33.2k23583
asked Jan 4 at 16:07
RwanouRwanou
737
737
Do your axles have recommended torque values printed on? I'd also contact the shop that sold your bike about torque affecting the alignment, that's not supposed to happen and might be a warranty/service case.
– Klaster_1
Jan 4 at 16:36
1
I don’t think they are mentioned, anyway, the axles come with a handle to easily remove a wheel on the side of the road, i couldn’t check the exact torque if I have a puncture during a ride.
– Rwanou
Jan 4 at 21:35
add a comment |
Do your axles have recommended torque values printed on? I'd also contact the shop that sold your bike about torque affecting the alignment, that's not supposed to happen and might be a warranty/service case.
– Klaster_1
Jan 4 at 16:36
1
I don’t think they are mentioned, anyway, the axles come with a handle to easily remove a wheel on the side of the road, i couldn’t check the exact torque if I have a puncture during a ride.
– Rwanou
Jan 4 at 21:35
Do your axles have recommended torque values printed on? I'd also contact the shop that sold your bike about torque affecting the alignment, that's not supposed to happen and might be a warranty/service case.
– Klaster_1
Jan 4 at 16:36
Do your axles have recommended torque values printed on? I'd also contact the shop that sold your bike about torque affecting the alignment, that's not supposed to happen and might be a warranty/service case.
– Klaster_1
Jan 4 at 16:36
1
1
I don’t think they are mentioned, anyway, the axles come with a handle to easily remove a wheel on the side of the road, i couldn’t check the exact torque if I have a puncture during a ride.
– Rwanou
Jan 4 at 21:35
I don’t think they are mentioned, anyway, the axles come with a handle to easily remove a wheel on the side of the road, i couldn’t check the exact torque if I have a puncture during a ride.
– Rwanou
Jan 4 at 21:35
add a comment |
2 Answers
2
active
oldest
votes
You should screw your through axle according to the manufacturer's specified torque value range. The torque applied to the axle is not meant to be used for adjusting relative brake/disc position, even if you observe such effect. Keeping the axle under-torqued is dangerous, and over-torquing it might damage the fork/frame dropouts.
A proper solution would be to adjust the position of the brake caliper itself relative to the disc. One possible way to achieve that:
- Screw the wheel's axle to manufacturer's recommended torque.
- Loosen both bolts that attach the caliper to the fork/frame. Do not unscrew them too much; you should just be able to wobble the caliper by hand.
- Squeeze the brake lever so that both pads hug the disc. If the pads were symmetric, then the caliper would become centered relative to the disc. In your case, you should probably do this with a new pair of pads.
- Keeping the lever pressed (by using a rubber band, rope etc.), tighten the caliper bolts so that the caliper will stay in the new position. Make sure to tighten these bolts to a proper torque as well (typically in a range 7-9 N×m, but it may be different)
Now, when you release the brake lever, the distance between pads and disc surfaces will be equal (given that both pads move at the same rate, of course).
You can also use some pair of spacers between pads and the disc (like thick paper bits), loosen the caliper bolts, squeeze and release the brake lever, then re-tighten the caliper.
– Grigory Rechistov
Jan 4 at 16:40
What is the purpose of the paper? It should bring the calliper in the exact same position as the first method.
– Carel
Jan 4 at 18:32
I don’t really want to start readjusting my flat mounts hydrolic disc brakes every time I remove the back wheel for cleaning. I’m not even sure Ultegra brakes allow any travel prior to tighting them.
– Rwanou
Jan 4 at 21:39
1
@gschenk - I was wondering the same thing, my bike's axles have traditional quick release levers, I have no torque wrench that would fit them. I just made it about as hard to close as a regular skewer based QR lever.
– Johnny
Jan 4 at 22:35
1
@Johnny I've read in the meantime that handle-less through axles (TA) with a hex interface are available. Some bikes might have such TA from the outset. Perhaps Grigory meant these?
– gschenk
Jan 4 at 22:54
|
show 4 more comments
I suspect a little that it was loose at one point and there won't be much movement of the brake within the thru-axle's window of "good" torque values. In other words, the range given for allen-headed "stealth" type thru axles, the only type that readily take a torque wrench, is usually about 9-13Nm, and I doubt there would be movement of the brake without about that range.
Torque it so that it's firmly bottomed out and you can feel there's heavy resistance to further preloading of the threads. Make sure there's some grease on the threads to make it easier to sense what's going on. The nature of big coarse aluminum threads actually makes it pretty clear to tell through wrench feel when you've reached the "bottomed out" point.
If it's still vague and you're having trouble with the brake wanting to move, that's unfortunate. Make sure the hub isn't missing any hardware and that any removable bits of the dropouts are tight. Finally, you can use a marker to make an index mark to set the rotational position of the axle to every time. For example, on the drive side where the end of the axle is visible when installed, you could draw a line across its face and onto the dropouts. You still have to make sure it's tight when you reinstall it in case something shifts/wears, but for the most part that should make it easy to reproduce the "adjustment."
Th OP says his axle comes with a handle (mine does too). I doubt he can use a torque wrench with that. Mine axle does have 10Nm printed but I don't know how could I check that and I understand the OP is also asking about that. How can he set the torque? In my case I already had to claim the warranty due to broken dropout-fork connection. It was accepted so probably not my fault, but doubts remain...
– Vladimir F
Jan 7 at 9:07
Hope you weren't hurt, but I doubt anything anyone did with the thru-axle caused that joint to fail. The only type of thru-axle that can easily be checked for torque are ones that have some kind of allen fitting, such as copies of the Maxle Stealth design or ones like the DT RWS Plug In axles that have lever that pops in and out of an allen fitting. If yours has a torque spec, it might be a type that the handles pops out of in some sneaky way.
– Nathan Knutson
Jan 7 at 9:30
That's what I actually do for the moment. I use the handle position as a marquer of my previous setting. The handle actually pulls and rotate so you can position it where you want without tightening. I guess I'll need to find the right torque by visually checking the position of the disk between the pads, then put the handle in a notable position (e.g. along the chain stay).
– Rwanou
Jan 7 at 10:22
Just to be clear, the is no movement of the any parts on the bike. It rides like a charm and my breaking is good, no loose parts or anything. It's just that tightening slightly more or slightly less will position the disc between the pads rather closer to the right or to the left, thus having an uneven wear of the disc pads. We are talking of less than 1 mm of difference, the pads being 2mm thick, difference is noticeable.
– Rwanou
Jan 7 at 10:32
If this problem doesn't go away no matter what you do, it unfortunately makes me suspect dropout misalignment, which there's currently to my knowledge no great off the shelf way to check on thru axle frames.
– Nathan Knutson
Jan 7 at 19:39
add a comment |
Your Answer
StackExchange.ready(function() {
var channelOptions = {
tags: "".split(" "),
id: "126"
};
initTagRenderer("".split(" "), "".split(" "), channelOptions);
StackExchange.using("externalEditor", function() {
// Have to fire editor after snippets, if snippets enabled
if (StackExchange.settings.snippets.snippetsEnabled) {
StackExchange.using("snippets", function() {
createEditor();
});
}
else {
createEditor();
}
});
function createEditor() {
StackExchange.prepareEditor({
heartbeatType: 'answer',
autoActivateHeartbeat: false,
convertImagesToLinks: false,
noModals: true,
showLowRepImageUploadWarning: true,
reputationToPostImages: null,
bindNavPrevention: true,
postfix: "",
imageUploader: {
brandingHtml: "Powered by u003ca class="icon-imgur-white" href="https://imgur.com/"u003eu003c/au003e",
contentPolicyHtml: "User contributions licensed under u003ca href="https://creativecommons.org/licenses/by-sa/3.0/"u003ecc by-sa 3.0 with attribution requiredu003c/au003e u003ca href="https://stackoverflow.com/legal/content-policy"u003e(content policy)u003c/au003e",
allowUrls: true
},
noCode: true, onDemand: true,
discardSelector: ".discard-answer"
,immediatelyShowMarkdownHelp:true
});
}
});
Sign up or log in
StackExchange.ready(function () {
StackExchange.helpers.onClickDraftSave('#login-link');
});
Sign up using Google
Sign up using Facebook
Sign up using Email and Password
Post as a guest
Required, but never shown
StackExchange.ready(
function () {
StackExchange.openid.initPostLogin('.new-post-login', 'https%3a%2f%2fbicycles.stackexchange.com%2fquestions%2f58760%2fhow-tight-should-i-screw-my-thru-axles%23new-answer', 'question_page');
}
);
Post as a guest
Required, but never shown
2 Answers
2
active
oldest
votes
2 Answers
2
active
oldest
votes
active
oldest
votes
active
oldest
votes
You should screw your through axle according to the manufacturer's specified torque value range. The torque applied to the axle is not meant to be used for adjusting relative brake/disc position, even if you observe such effect. Keeping the axle under-torqued is dangerous, and over-torquing it might damage the fork/frame dropouts.
A proper solution would be to adjust the position of the brake caliper itself relative to the disc. One possible way to achieve that:
- Screw the wheel's axle to manufacturer's recommended torque.
- Loosen both bolts that attach the caliper to the fork/frame. Do not unscrew them too much; you should just be able to wobble the caliper by hand.
- Squeeze the brake lever so that both pads hug the disc. If the pads were symmetric, then the caliper would become centered relative to the disc. In your case, you should probably do this with a new pair of pads.
- Keeping the lever pressed (by using a rubber band, rope etc.), tighten the caliper bolts so that the caliper will stay in the new position. Make sure to tighten these bolts to a proper torque as well (typically in a range 7-9 N×m, but it may be different)
Now, when you release the brake lever, the distance between pads and disc surfaces will be equal (given that both pads move at the same rate, of course).
You can also use some pair of spacers between pads and the disc (like thick paper bits), loosen the caliper bolts, squeeze and release the brake lever, then re-tighten the caliper.
– Grigory Rechistov
Jan 4 at 16:40
What is the purpose of the paper? It should bring the calliper in the exact same position as the first method.
– Carel
Jan 4 at 18:32
I don’t really want to start readjusting my flat mounts hydrolic disc brakes every time I remove the back wheel for cleaning. I’m not even sure Ultegra brakes allow any travel prior to tighting them.
– Rwanou
Jan 4 at 21:39
1
@gschenk - I was wondering the same thing, my bike's axles have traditional quick release levers, I have no torque wrench that would fit them. I just made it about as hard to close as a regular skewer based QR lever.
– Johnny
Jan 4 at 22:35
1
@Johnny I've read in the meantime that handle-less through axles (TA) with a hex interface are available. Some bikes might have such TA from the outset. Perhaps Grigory meant these?
– gschenk
Jan 4 at 22:54
|
show 4 more comments
You should screw your through axle according to the manufacturer's specified torque value range. The torque applied to the axle is not meant to be used for adjusting relative brake/disc position, even if you observe such effect. Keeping the axle under-torqued is dangerous, and over-torquing it might damage the fork/frame dropouts.
A proper solution would be to adjust the position of the brake caliper itself relative to the disc. One possible way to achieve that:
- Screw the wheel's axle to manufacturer's recommended torque.
- Loosen both bolts that attach the caliper to the fork/frame. Do not unscrew them too much; you should just be able to wobble the caliper by hand.
- Squeeze the brake lever so that both pads hug the disc. If the pads were symmetric, then the caliper would become centered relative to the disc. In your case, you should probably do this with a new pair of pads.
- Keeping the lever pressed (by using a rubber band, rope etc.), tighten the caliper bolts so that the caliper will stay in the new position. Make sure to tighten these bolts to a proper torque as well (typically in a range 7-9 N×m, but it may be different)
Now, when you release the brake lever, the distance between pads and disc surfaces will be equal (given that both pads move at the same rate, of course).
You can also use some pair of spacers between pads and the disc (like thick paper bits), loosen the caliper bolts, squeeze and release the brake lever, then re-tighten the caliper.
– Grigory Rechistov
Jan 4 at 16:40
What is the purpose of the paper? It should bring the calliper in the exact same position as the first method.
– Carel
Jan 4 at 18:32
I don’t really want to start readjusting my flat mounts hydrolic disc brakes every time I remove the back wheel for cleaning. I’m not even sure Ultegra brakes allow any travel prior to tighting them.
– Rwanou
Jan 4 at 21:39
1
@gschenk - I was wondering the same thing, my bike's axles have traditional quick release levers, I have no torque wrench that would fit them. I just made it about as hard to close as a regular skewer based QR lever.
– Johnny
Jan 4 at 22:35
1
@Johnny I've read in the meantime that handle-less through axles (TA) with a hex interface are available. Some bikes might have such TA from the outset. Perhaps Grigory meant these?
– gschenk
Jan 4 at 22:54
|
show 4 more comments
You should screw your through axle according to the manufacturer's specified torque value range. The torque applied to the axle is not meant to be used for adjusting relative brake/disc position, even if you observe such effect. Keeping the axle under-torqued is dangerous, and over-torquing it might damage the fork/frame dropouts.
A proper solution would be to adjust the position of the brake caliper itself relative to the disc. One possible way to achieve that:
- Screw the wheel's axle to manufacturer's recommended torque.
- Loosen both bolts that attach the caliper to the fork/frame. Do not unscrew them too much; you should just be able to wobble the caliper by hand.
- Squeeze the brake lever so that both pads hug the disc. If the pads were symmetric, then the caliper would become centered relative to the disc. In your case, you should probably do this with a new pair of pads.
- Keeping the lever pressed (by using a rubber band, rope etc.), tighten the caliper bolts so that the caliper will stay in the new position. Make sure to tighten these bolts to a proper torque as well (typically in a range 7-9 N×m, but it may be different)
Now, when you release the brake lever, the distance between pads and disc surfaces will be equal (given that both pads move at the same rate, of course).
You should screw your through axle according to the manufacturer's specified torque value range. The torque applied to the axle is not meant to be used for adjusting relative brake/disc position, even if you observe such effect. Keeping the axle under-torqued is dangerous, and over-torquing it might damage the fork/frame dropouts.
A proper solution would be to adjust the position of the brake caliper itself relative to the disc. One possible way to achieve that:
- Screw the wheel's axle to manufacturer's recommended torque.
- Loosen both bolts that attach the caliper to the fork/frame. Do not unscrew them too much; you should just be able to wobble the caliper by hand.
- Squeeze the brake lever so that both pads hug the disc. If the pads were symmetric, then the caliper would become centered relative to the disc. In your case, you should probably do this with a new pair of pads.
- Keeping the lever pressed (by using a rubber band, rope etc.), tighten the caliper bolts so that the caliper will stay in the new position. Make sure to tighten these bolts to a proper torque as well (typically in a range 7-9 N×m, but it may be different)
Now, when you release the brake lever, the distance between pads and disc surfaces will be equal (given that both pads move at the same rate, of course).
answered Jan 4 at 16:36
Grigory RechistovGrigory Rechistov
4,526829
4,526829
You can also use some pair of spacers between pads and the disc (like thick paper bits), loosen the caliper bolts, squeeze and release the brake lever, then re-tighten the caliper.
– Grigory Rechistov
Jan 4 at 16:40
What is the purpose of the paper? It should bring the calliper in the exact same position as the first method.
– Carel
Jan 4 at 18:32
I don’t really want to start readjusting my flat mounts hydrolic disc brakes every time I remove the back wheel for cleaning. I’m not even sure Ultegra brakes allow any travel prior to tighting them.
– Rwanou
Jan 4 at 21:39
1
@gschenk - I was wondering the same thing, my bike's axles have traditional quick release levers, I have no torque wrench that would fit them. I just made it about as hard to close as a regular skewer based QR lever.
– Johnny
Jan 4 at 22:35
1
@Johnny I've read in the meantime that handle-less through axles (TA) with a hex interface are available. Some bikes might have such TA from the outset. Perhaps Grigory meant these?
– gschenk
Jan 4 at 22:54
|
show 4 more comments
You can also use some pair of spacers between pads and the disc (like thick paper bits), loosen the caliper bolts, squeeze and release the brake lever, then re-tighten the caliper.
– Grigory Rechistov
Jan 4 at 16:40
What is the purpose of the paper? It should bring the calliper in the exact same position as the first method.
– Carel
Jan 4 at 18:32
I don’t really want to start readjusting my flat mounts hydrolic disc brakes every time I remove the back wheel for cleaning. I’m not even sure Ultegra brakes allow any travel prior to tighting them.
– Rwanou
Jan 4 at 21:39
1
@gschenk - I was wondering the same thing, my bike's axles have traditional quick release levers, I have no torque wrench that would fit them. I just made it about as hard to close as a regular skewer based QR lever.
– Johnny
Jan 4 at 22:35
1
@Johnny I've read in the meantime that handle-less through axles (TA) with a hex interface are available. Some bikes might have such TA from the outset. Perhaps Grigory meant these?
– gschenk
Jan 4 at 22:54
You can also use some pair of spacers between pads and the disc (like thick paper bits), loosen the caliper bolts, squeeze and release the brake lever, then re-tighten the caliper.
– Grigory Rechistov
Jan 4 at 16:40
You can also use some pair of spacers between pads and the disc (like thick paper bits), loosen the caliper bolts, squeeze and release the brake lever, then re-tighten the caliper.
– Grigory Rechistov
Jan 4 at 16:40
What is the purpose of the paper? It should bring the calliper in the exact same position as the first method.
– Carel
Jan 4 at 18:32
What is the purpose of the paper? It should bring the calliper in the exact same position as the first method.
– Carel
Jan 4 at 18:32
I don’t really want to start readjusting my flat mounts hydrolic disc brakes every time I remove the back wheel for cleaning. I’m not even sure Ultegra brakes allow any travel prior to tighting them.
– Rwanou
Jan 4 at 21:39
I don’t really want to start readjusting my flat mounts hydrolic disc brakes every time I remove the back wheel for cleaning. I’m not even sure Ultegra brakes allow any travel prior to tighting them.
– Rwanou
Jan 4 at 21:39
1
1
@gschenk - I was wondering the same thing, my bike's axles have traditional quick release levers, I have no torque wrench that would fit them. I just made it about as hard to close as a regular skewer based QR lever.
– Johnny
Jan 4 at 22:35
@gschenk - I was wondering the same thing, my bike's axles have traditional quick release levers, I have no torque wrench that would fit them. I just made it about as hard to close as a regular skewer based QR lever.
– Johnny
Jan 4 at 22:35
1
1
@Johnny I've read in the meantime that handle-less through axles (TA) with a hex interface are available. Some bikes might have such TA from the outset. Perhaps Grigory meant these?
– gschenk
Jan 4 at 22:54
@Johnny I've read in the meantime that handle-less through axles (TA) with a hex interface are available. Some bikes might have such TA from the outset. Perhaps Grigory meant these?
– gschenk
Jan 4 at 22:54
|
show 4 more comments
I suspect a little that it was loose at one point and there won't be much movement of the brake within the thru-axle's window of "good" torque values. In other words, the range given for allen-headed "stealth" type thru axles, the only type that readily take a torque wrench, is usually about 9-13Nm, and I doubt there would be movement of the brake without about that range.
Torque it so that it's firmly bottomed out and you can feel there's heavy resistance to further preloading of the threads. Make sure there's some grease on the threads to make it easier to sense what's going on. The nature of big coarse aluminum threads actually makes it pretty clear to tell through wrench feel when you've reached the "bottomed out" point.
If it's still vague and you're having trouble with the brake wanting to move, that's unfortunate. Make sure the hub isn't missing any hardware and that any removable bits of the dropouts are tight. Finally, you can use a marker to make an index mark to set the rotational position of the axle to every time. For example, on the drive side where the end of the axle is visible when installed, you could draw a line across its face and onto the dropouts. You still have to make sure it's tight when you reinstall it in case something shifts/wears, but for the most part that should make it easy to reproduce the "adjustment."
Th OP says his axle comes with a handle (mine does too). I doubt he can use a torque wrench with that. Mine axle does have 10Nm printed but I don't know how could I check that and I understand the OP is also asking about that. How can he set the torque? In my case I already had to claim the warranty due to broken dropout-fork connection. It was accepted so probably not my fault, but doubts remain...
– Vladimir F
Jan 7 at 9:07
Hope you weren't hurt, but I doubt anything anyone did with the thru-axle caused that joint to fail. The only type of thru-axle that can easily be checked for torque are ones that have some kind of allen fitting, such as copies of the Maxle Stealth design or ones like the DT RWS Plug In axles that have lever that pops in and out of an allen fitting. If yours has a torque spec, it might be a type that the handles pops out of in some sneaky way.
– Nathan Knutson
Jan 7 at 9:30
That's what I actually do for the moment. I use the handle position as a marquer of my previous setting. The handle actually pulls and rotate so you can position it where you want without tightening. I guess I'll need to find the right torque by visually checking the position of the disk between the pads, then put the handle in a notable position (e.g. along the chain stay).
– Rwanou
Jan 7 at 10:22
Just to be clear, the is no movement of the any parts on the bike. It rides like a charm and my breaking is good, no loose parts or anything. It's just that tightening slightly more or slightly less will position the disc between the pads rather closer to the right or to the left, thus having an uneven wear of the disc pads. We are talking of less than 1 mm of difference, the pads being 2mm thick, difference is noticeable.
– Rwanou
Jan 7 at 10:32
If this problem doesn't go away no matter what you do, it unfortunately makes me suspect dropout misalignment, which there's currently to my knowledge no great off the shelf way to check on thru axle frames.
– Nathan Knutson
Jan 7 at 19:39
add a comment |
I suspect a little that it was loose at one point and there won't be much movement of the brake within the thru-axle's window of "good" torque values. In other words, the range given for allen-headed "stealth" type thru axles, the only type that readily take a torque wrench, is usually about 9-13Nm, and I doubt there would be movement of the brake without about that range.
Torque it so that it's firmly bottomed out and you can feel there's heavy resistance to further preloading of the threads. Make sure there's some grease on the threads to make it easier to sense what's going on. The nature of big coarse aluminum threads actually makes it pretty clear to tell through wrench feel when you've reached the "bottomed out" point.
If it's still vague and you're having trouble with the brake wanting to move, that's unfortunate. Make sure the hub isn't missing any hardware and that any removable bits of the dropouts are tight. Finally, you can use a marker to make an index mark to set the rotational position of the axle to every time. For example, on the drive side where the end of the axle is visible when installed, you could draw a line across its face and onto the dropouts. You still have to make sure it's tight when you reinstall it in case something shifts/wears, but for the most part that should make it easy to reproduce the "adjustment."
Th OP says his axle comes with a handle (mine does too). I doubt he can use a torque wrench with that. Mine axle does have 10Nm printed but I don't know how could I check that and I understand the OP is also asking about that. How can he set the torque? In my case I already had to claim the warranty due to broken dropout-fork connection. It was accepted so probably not my fault, but doubts remain...
– Vladimir F
Jan 7 at 9:07
Hope you weren't hurt, but I doubt anything anyone did with the thru-axle caused that joint to fail. The only type of thru-axle that can easily be checked for torque are ones that have some kind of allen fitting, such as copies of the Maxle Stealth design or ones like the DT RWS Plug In axles that have lever that pops in and out of an allen fitting. If yours has a torque spec, it might be a type that the handles pops out of in some sneaky way.
– Nathan Knutson
Jan 7 at 9:30
That's what I actually do for the moment. I use the handle position as a marquer of my previous setting. The handle actually pulls and rotate so you can position it where you want without tightening. I guess I'll need to find the right torque by visually checking the position of the disk between the pads, then put the handle in a notable position (e.g. along the chain stay).
– Rwanou
Jan 7 at 10:22
Just to be clear, the is no movement of the any parts on the bike. It rides like a charm and my breaking is good, no loose parts or anything. It's just that tightening slightly more or slightly less will position the disc between the pads rather closer to the right or to the left, thus having an uneven wear of the disc pads. We are talking of less than 1 mm of difference, the pads being 2mm thick, difference is noticeable.
– Rwanou
Jan 7 at 10:32
If this problem doesn't go away no matter what you do, it unfortunately makes me suspect dropout misalignment, which there's currently to my knowledge no great off the shelf way to check on thru axle frames.
– Nathan Knutson
Jan 7 at 19:39
add a comment |
I suspect a little that it was loose at one point and there won't be much movement of the brake within the thru-axle's window of "good" torque values. In other words, the range given for allen-headed "stealth" type thru axles, the only type that readily take a torque wrench, is usually about 9-13Nm, and I doubt there would be movement of the brake without about that range.
Torque it so that it's firmly bottomed out and you can feel there's heavy resistance to further preloading of the threads. Make sure there's some grease on the threads to make it easier to sense what's going on. The nature of big coarse aluminum threads actually makes it pretty clear to tell through wrench feel when you've reached the "bottomed out" point.
If it's still vague and you're having trouble with the brake wanting to move, that's unfortunate. Make sure the hub isn't missing any hardware and that any removable bits of the dropouts are tight. Finally, you can use a marker to make an index mark to set the rotational position of the axle to every time. For example, on the drive side where the end of the axle is visible when installed, you could draw a line across its face and onto the dropouts. You still have to make sure it's tight when you reinstall it in case something shifts/wears, but for the most part that should make it easy to reproduce the "adjustment."
I suspect a little that it was loose at one point and there won't be much movement of the brake within the thru-axle's window of "good" torque values. In other words, the range given for allen-headed "stealth" type thru axles, the only type that readily take a torque wrench, is usually about 9-13Nm, and I doubt there would be movement of the brake without about that range.
Torque it so that it's firmly bottomed out and you can feel there's heavy resistance to further preloading of the threads. Make sure there's some grease on the threads to make it easier to sense what's going on. The nature of big coarse aluminum threads actually makes it pretty clear to tell through wrench feel when you've reached the "bottomed out" point.
If it's still vague and you're having trouble with the brake wanting to move, that's unfortunate. Make sure the hub isn't missing any hardware and that any removable bits of the dropouts are tight. Finally, you can use a marker to make an index mark to set the rotational position of the axle to every time. For example, on the drive side where the end of the axle is visible when installed, you could draw a line across its face and onto the dropouts. You still have to make sure it's tight when you reinstall it in case something shifts/wears, but for the most part that should make it easy to reproduce the "adjustment."
edited Jan 5 at 2:39
answered Jan 5 at 2:24
Nathan KnutsonNathan Knutson
23.1k11958
23.1k11958
Th OP says his axle comes with a handle (mine does too). I doubt he can use a torque wrench with that. Mine axle does have 10Nm printed but I don't know how could I check that and I understand the OP is also asking about that. How can he set the torque? In my case I already had to claim the warranty due to broken dropout-fork connection. It was accepted so probably not my fault, but doubts remain...
– Vladimir F
Jan 7 at 9:07
Hope you weren't hurt, but I doubt anything anyone did with the thru-axle caused that joint to fail. The only type of thru-axle that can easily be checked for torque are ones that have some kind of allen fitting, such as copies of the Maxle Stealth design or ones like the DT RWS Plug In axles that have lever that pops in and out of an allen fitting. If yours has a torque spec, it might be a type that the handles pops out of in some sneaky way.
– Nathan Knutson
Jan 7 at 9:30
That's what I actually do for the moment. I use the handle position as a marquer of my previous setting. The handle actually pulls and rotate so you can position it where you want without tightening. I guess I'll need to find the right torque by visually checking the position of the disk between the pads, then put the handle in a notable position (e.g. along the chain stay).
– Rwanou
Jan 7 at 10:22
Just to be clear, the is no movement of the any parts on the bike. It rides like a charm and my breaking is good, no loose parts or anything. It's just that tightening slightly more or slightly less will position the disc between the pads rather closer to the right or to the left, thus having an uneven wear of the disc pads. We are talking of less than 1 mm of difference, the pads being 2mm thick, difference is noticeable.
– Rwanou
Jan 7 at 10:32
If this problem doesn't go away no matter what you do, it unfortunately makes me suspect dropout misalignment, which there's currently to my knowledge no great off the shelf way to check on thru axle frames.
– Nathan Knutson
Jan 7 at 19:39
add a comment |
Th OP says his axle comes with a handle (mine does too). I doubt he can use a torque wrench with that. Mine axle does have 10Nm printed but I don't know how could I check that and I understand the OP is also asking about that. How can he set the torque? In my case I already had to claim the warranty due to broken dropout-fork connection. It was accepted so probably not my fault, but doubts remain...
– Vladimir F
Jan 7 at 9:07
Hope you weren't hurt, but I doubt anything anyone did with the thru-axle caused that joint to fail. The only type of thru-axle that can easily be checked for torque are ones that have some kind of allen fitting, such as copies of the Maxle Stealth design or ones like the DT RWS Plug In axles that have lever that pops in and out of an allen fitting. If yours has a torque spec, it might be a type that the handles pops out of in some sneaky way.
– Nathan Knutson
Jan 7 at 9:30
That's what I actually do for the moment. I use the handle position as a marquer of my previous setting. The handle actually pulls and rotate so you can position it where you want without tightening. I guess I'll need to find the right torque by visually checking the position of the disk between the pads, then put the handle in a notable position (e.g. along the chain stay).
– Rwanou
Jan 7 at 10:22
Just to be clear, the is no movement of the any parts on the bike. It rides like a charm and my breaking is good, no loose parts or anything. It's just that tightening slightly more or slightly less will position the disc between the pads rather closer to the right or to the left, thus having an uneven wear of the disc pads. We are talking of less than 1 mm of difference, the pads being 2mm thick, difference is noticeable.
– Rwanou
Jan 7 at 10:32
If this problem doesn't go away no matter what you do, it unfortunately makes me suspect dropout misalignment, which there's currently to my knowledge no great off the shelf way to check on thru axle frames.
– Nathan Knutson
Jan 7 at 19:39
Th OP says his axle comes with a handle (mine does too). I doubt he can use a torque wrench with that. Mine axle does have 10Nm printed but I don't know how could I check that and I understand the OP is also asking about that. How can he set the torque? In my case I already had to claim the warranty due to broken dropout-fork connection. It was accepted so probably not my fault, but doubts remain...
– Vladimir F
Jan 7 at 9:07
Th OP says his axle comes with a handle (mine does too). I doubt he can use a torque wrench with that. Mine axle does have 10Nm printed but I don't know how could I check that and I understand the OP is also asking about that. How can he set the torque? In my case I already had to claim the warranty due to broken dropout-fork connection. It was accepted so probably not my fault, but doubts remain...
– Vladimir F
Jan 7 at 9:07
Hope you weren't hurt, but I doubt anything anyone did with the thru-axle caused that joint to fail. The only type of thru-axle that can easily be checked for torque are ones that have some kind of allen fitting, such as copies of the Maxle Stealth design or ones like the DT RWS Plug In axles that have lever that pops in and out of an allen fitting. If yours has a torque spec, it might be a type that the handles pops out of in some sneaky way.
– Nathan Knutson
Jan 7 at 9:30
Hope you weren't hurt, but I doubt anything anyone did with the thru-axle caused that joint to fail. The only type of thru-axle that can easily be checked for torque are ones that have some kind of allen fitting, such as copies of the Maxle Stealth design or ones like the DT RWS Plug In axles that have lever that pops in and out of an allen fitting. If yours has a torque spec, it might be a type that the handles pops out of in some sneaky way.
– Nathan Knutson
Jan 7 at 9:30
That's what I actually do for the moment. I use the handle position as a marquer of my previous setting. The handle actually pulls and rotate so you can position it where you want without tightening. I guess I'll need to find the right torque by visually checking the position of the disk between the pads, then put the handle in a notable position (e.g. along the chain stay).
– Rwanou
Jan 7 at 10:22
That's what I actually do for the moment. I use the handle position as a marquer of my previous setting. The handle actually pulls and rotate so you can position it where you want without tightening. I guess I'll need to find the right torque by visually checking the position of the disk between the pads, then put the handle in a notable position (e.g. along the chain stay).
– Rwanou
Jan 7 at 10:22
Just to be clear, the is no movement of the any parts on the bike. It rides like a charm and my breaking is good, no loose parts or anything. It's just that tightening slightly more or slightly less will position the disc between the pads rather closer to the right or to the left, thus having an uneven wear of the disc pads. We are talking of less than 1 mm of difference, the pads being 2mm thick, difference is noticeable.
– Rwanou
Jan 7 at 10:32
Just to be clear, the is no movement of the any parts on the bike. It rides like a charm and my breaking is good, no loose parts or anything. It's just that tightening slightly more or slightly less will position the disc between the pads rather closer to the right or to the left, thus having an uneven wear of the disc pads. We are talking of less than 1 mm of difference, the pads being 2mm thick, difference is noticeable.
– Rwanou
Jan 7 at 10:32
If this problem doesn't go away no matter what you do, it unfortunately makes me suspect dropout misalignment, which there's currently to my knowledge no great off the shelf way to check on thru axle frames.
– Nathan Knutson
Jan 7 at 19:39
If this problem doesn't go away no matter what you do, it unfortunately makes me suspect dropout misalignment, which there's currently to my knowledge no great off the shelf way to check on thru axle frames.
– Nathan Knutson
Jan 7 at 19:39
add a comment |
Thanks for contributing an answer to Bicycles Stack Exchange!
- Please be sure to answer the question. Provide details and share your research!
But avoid …
- Asking for help, clarification, or responding to other answers.
- Making statements based on opinion; back them up with references or personal experience.
To learn more, see our tips on writing great answers.
Sign up or log in
StackExchange.ready(function () {
StackExchange.helpers.onClickDraftSave('#login-link');
});
Sign up using Google
Sign up using Facebook
Sign up using Email and Password
Post as a guest
Required, but never shown
StackExchange.ready(
function () {
StackExchange.openid.initPostLogin('.new-post-login', 'https%3a%2f%2fbicycles.stackexchange.com%2fquestions%2f58760%2fhow-tight-should-i-screw-my-thru-axles%23new-answer', 'question_page');
}
);
Post as a guest
Required, but never shown
Sign up or log in
StackExchange.ready(function () {
StackExchange.helpers.onClickDraftSave('#login-link');
});
Sign up using Google
Sign up using Facebook
Sign up using Email and Password
Post as a guest
Required, but never shown
Sign up or log in
StackExchange.ready(function () {
StackExchange.helpers.onClickDraftSave('#login-link');
});
Sign up using Google
Sign up using Facebook
Sign up using Email and Password
Post as a guest
Required, but never shown
Sign up or log in
StackExchange.ready(function () {
StackExchange.helpers.onClickDraftSave('#login-link');
});
Sign up using Google
Sign up using Facebook
Sign up using Email and Password
Sign up using Google
Sign up using Facebook
Sign up using Email and Password
Post as a guest
Required, but never shown
Required, but never shown
Required, but never shown
Required, but never shown
Required, but never shown
Required, but never shown
Required, but never shown
Required, but never shown
Required, but never shown
Io6OYFPa84IL7wM9PCh5tX,A3bPw,NdVgm7uHBwn,e9rXNfrmTF0jDL7LTMSI7MgQbtt1mOcBjMW
Do your axles have recommended torque values printed on? I'd also contact the shop that sold your bike about torque affecting the alignment, that's not supposed to happen and might be a warranty/service case.
– Klaster_1
Jan 4 at 16:36
1
I don’t think they are mentioned, anyway, the axles come with a handle to easily remove a wheel on the side of the road, i couldn’t check the exact torque if I have a puncture during a ride.
– Rwanou
Jan 4 at 21:35