Why would a jet engine that runs at temps excess of 2000°C burn when it crashes?
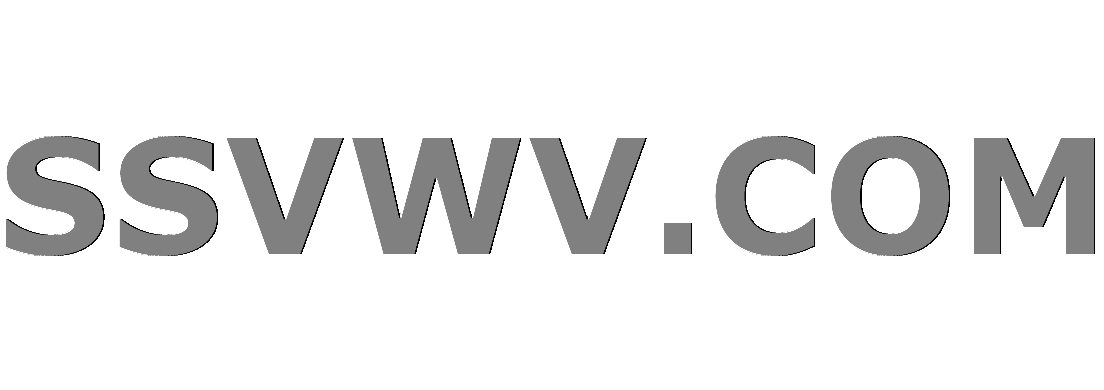
Multi tool use
$begingroup$
Airline engines are designed to work at very high temperatures. Yet, when a plane crashes they're burnt (see below). Is it something in their design?
(bostonherald.com)
jet-engine accidents aerospace-materials
$endgroup$
add a comment |
$begingroup$
Airline engines are designed to work at very high temperatures. Yet, when a plane crashes they're burnt (see below). Is it something in their design?
(bostonherald.com)
jet-engine accidents aerospace-materials
$endgroup$
9
$begingroup$
The engine in the photograph is not melted.
$endgroup$
– Michael Hall
Mar 12 at 23:10
2
$begingroup$
@MichaelHall: That's on me, I've fixed it. OP originally wrote burnt. Although judging by the LP section, it did melt.
$endgroup$
– ymb1
Mar 12 at 23:36
21
$begingroup$
I have to challenge the premise. From the picture, it looks like the external housing of the engine burned and/or melted. The internal parts look like they've just suffered impact damage. The external housing does not experience high temperatures. Same reason the combustion temperature of your car's engine may reach 2000 C or so, yet the plastic components sitting nearby don't melt.
$endgroup$
– jamesqf
Mar 13 at 4:25
$begingroup$
related: aviation.stackexchange.com/a/16842/1467
$endgroup$
– Federico♦
Mar 13 at 9:11
2
$begingroup$
I think that the only thing we can say about the external housing is that it is missing from the picture. Besides melting or burning away it could have broken up on impact and pieces shed away as the core slid along the ground. Tough to surmise what happened from a single still photo.
$endgroup$
– Michael Hall
Mar 13 at 16:54
add a comment |
$begingroup$
Airline engines are designed to work at very high temperatures. Yet, when a plane crashes they're burnt (see below). Is it something in their design?
(bostonherald.com)
jet-engine accidents aerospace-materials
$endgroup$
Airline engines are designed to work at very high temperatures. Yet, when a plane crashes they're burnt (see below). Is it something in their design?
(bostonherald.com)
jet-engine accidents aerospace-materials
jet-engine accidents aerospace-materials
edited Mar 12 at 23:35


ymb1
67.9k7215360
67.9k7215360
asked Mar 12 at 22:34


RegmiRegmi
30529
30529
9
$begingroup$
The engine in the photograph is not melted.
$endgroup$
– Michael Hall
Mar 12 at 23:10
2
$begingroup$
@MichaelHall: That's on me, I've fixed it. OP originally wrote burnt. Although judging by the LP section, it did melt.
$endgroup$
– ymb1
Mar 12 at 23:36
21
$begingroup$
I have to challenge the premise. From the picture, it looks like the external housing of the engine burned and/or melted. The internal parts look like they've just suffered impact damage. The external housing does not experience high temperatures. Same reason the combustion temperature of your car's engine may reach 2000 C or so, yet the plastic components sitting nearby don't melt.
$endgroup$
– jamesqf
Mar 13 at 4:25
$begingroup$
related: aviation.stackexchange.com/a/16842/1467
$endgroup$
– Federico♦
Mar 13 at 9:11
2
$begingroup$
I think that the only thing we can say about the external housing is that it is missing from the picture. Besides melting or burning away it could have broken up on impact and pieces shed away as the core slid along the ground. Tough to surmise what happened from a single still photo.
$endgroup$
– Michael Hall
Mar 13 at 16:54
add a comment |
9
$begingroup$
The engine in the photograph is not melted.
$endgroup$
– Michael Hall
Mar 12 at 23:10
2
$begingroup$
@MichaelHall: That's on me, I've fixed it. OP originally wrote burnt. Although judging by the LP section, it did melt.
$endgroup$
– ymb1
Mar 12 at 23:36
21
$begingroup$
I have to challenge the premise. From the picture, it looks like the external housing of the engine burned and/or melted. The internal parts look like they've just suffered impact damage. The external housing does not experience high temperatures. Same reason the combustion temperature of your car's engine may reach 2000 C or so, yet the plastic components sitting nearby don't melt.
$endgroup$
– jamesqf
Mar 13 at 4:25
$begingroup$
related: aviation.stackexchange.com/a/16842/1467
$endgroup$
– Federico♦
Mar 13 at 9:11
2
$begingroup$
I think that the only thing we can say about the external housing is that it is missing from the picture. Besides melting or burning away it could have broken up on impact and pieces shed away as the core slid along the ground. Tough to surmise what happened from a single still photo.
$endgroup$
– Michael Hall
Mar 13 at 16:54
9
9
$begingroup$
The engine in the photograph is not melted.
$endgroup$
– Michael Hall
Mar 12 at 23:10
$begingroup$
The engine in the photograph is not melted.
$endgroup$
– Michael Hall
Mar 12 at 23:10
2
2
$begingroup$
@MichaelHall: That's on me, I've fixed it. OP originally wrote burnt. Although judging by the LP section, it did melt.
$endgroup$
– ymb1
Mar 12 at 23:36
$begingroup$
@MichaelHall: That's on me, I've fixed it. OP originally wrote burnt. Although judging by the LP section, it did melt.
$endgroup$
– ymb1
Mar 12 at 23:36
21
21
$begingroup$
I have to challenge the premise. From the picture, it looks like the external housing of the engine burned and/or melted. The internal parts look like they've just suffered impact damage. The external housing does not experience high temperatures. Same reason the combustion temperature of your car's engine may reach 2000 C or so, yet the plastic components sitting nearby don't melt.
$endgroup$
– jamesqf
Mar 13 at 4:25
$begingroup$
I have to challenge the premise. From the picture, it looks like the external housing of the engine burned and/or melted. The internal parts look like they've just suffered impact damage. The external housing does not experience high temperatures. Same reason the combustion temperature of your car's engine may reach 2000 C or so, yet the plastic components sitting nearby don't melt.
$endgroup$
– jamesqf
Mar 13 at 4:25
$begingroup$
related: aviation.stackexchange.com/a/16842/1467
$endgroup$
– Federico♦
Mar 13 at 9:11
$begingroup$
related: aviation.stackexchange.com/a/16842/1467
$endgroup$
– Federico♦
Mar 13 at 9:11
2
2
$begingroup$
I think that the only thing we can say about the external housing is that it is missing from the picture. Besides melting or burning away it could have broken up on impact and pieces shed away as the core slid along the ground. Tough to surmise what happened from a single still photo.
$endgroup$
– Michael Hall
Mar 13 at 16:54
$begingroup$
I think that the only thing we can say about the external housing is that it is missing from the picture. Besides melting or burning away it could have broken up on impact and pieces shed away as the core slid along the ground. Tough to surmise what happened from a single still photo.
$endgroup$
– Michael Hall
Mar 13 at 16:54
add a comment |
3 Answers
3
active
oldest
votes
$begingroup$
How The Jet Engine Works:
Inside the typical commercial jet engine, the fuel burns in the combustion chamber at up to 2000 degrees Celsius. The temperature at which metals in this part of the engine start to melt is 1300 degrees Celsius, so advanced cooling techniques must be used.
You can read more about some of those cooling mechanisms in How are temperature differences handled in a jet engine?
See also, How do you stop a jet engine melting?:
Neil - The normal melting point of the nickel blade alloys that we use in the turbine is typically about 12-1400 degrees. But what you do, and this is the clever bit, is you actually cool these blades. You have internal cooling passages, which effectively has air that flows through and it's about 7-800 degrees. And this cooling air then exits from small little minute holes that have been drilled on the surface of the blade and this air then forms a kind of a film on the surface of the blade, and this technology is typically called a 'film cooling.'
What you also do - you coat these blades and typically use something called a thermal barrier coating. The thermal barrier coating, effectively, is ceramic, typically about quarter of a millimeter in thickness, but they have got very, very low thermal conductivity. So, effectively, even though the gas stream is at a much higher air temperature, the effective metal that exists beneath the thermal barrier coating is much colder, and you get thermal grade of the order of about 100 degrees C between the hot and the cold surface. So all of this put together - this whole cooling technology effectively helps to keep the blade below its melting temperature.
The engine is designed to manage the intense heat in a controlled way, by restricting it to certain components, injecting cool air around the hot parts, and choosing different materials for different parts of the engine. If the engine is severely damaged, doused in jet fuel, and set on fire, none of those mechanisms function; the entire engine (or whatever is left of it), as opposed to just the portions intended to manage heat, will be hot, and none of the cooling mechanisms will be working.
$endgroup$
$begingroup$
Those blades are little marvels of engineering. Something you can hold in one hand but costs some ~5000 dollars (and there's a whole lot of them in one turbine)
$endgroup$
– mbrig
Mar 13 at 2:37
2
$begingroup$
@Dannie Yes, turbine blades can be handled with your bare hands and used. The metals are nickle based super alloys and they sometime have a ceramic thermal barrier coating they are very environmentally stable. When assembling an engine, they actually use beeswax to hold seals in place and it just burns off once the engine is ran.
$endgroup$
– OSUZorba
Mar 14 at 4:13
1
$begingroup$
I'd like to add, that although the superalloys can make it to ~1400C before they melt, they will oxidize ("burn") at lower temperatures. The picture to me looks mostly like impact damage to me with some oxidization. Part of the reason it looks like impact damage to me is that materials with low melting/oxidation points are still there, but then materials with very high melting points are not.
$endgroup$
– OSUZorba
Mar 14 at 4:30
2
$begingroup$
So you're telling me that a jet engine actually operates above the melting point of the turbine blades? And that they are kept solid by some sophisticated aerodynamics? And if that fails, the entire engine will presumably turn into a blob of lava? I wish I hadn't read that now...
$endgroup$
– Oscar Bravo
Mar 14 at 7:35
1
$begingroup$
@OSUZorba it's even cleverer than that. The surface isn't the same as the bulk, but a thin layer of nickel aluminide (some blades anyway) with a high thermal conductivity and high melting point (~1600-1900C). This reacts in service to form Al2O3 (sapphire), MP ~2000C, but if blades are overhauled the sapphire must be removed before recoating. Paper from some former colleagues of mine. I've handled the blades in question, which I believe were miltary.
$endgroup$
– Chris H
Mar 14 at 9:23
|
show 4 more comments
$begingroup$
Peter's answer to another question has a nice chart that shows internal jet engine temperatures:
You can see that the temperatures are highest by a fairly large factor in the combustion chamber. This means that only the combustion chamber needs to be able to withstand those temperatures. To save weight and often use less expensive and less exotic materials, the rest of the engine may be made out of materials that don't need to withstand such high temperatures. As such, in an accident where jet fuel may be dispersed in an uncontrolled way and burn with as much oxygen as it can get, it's easy to scorch engine parts and anything else around.
It also is in part a question of time. The ability to withstand heat varies with time. In a crash of a fairly fueled aircraft that may burn uncontrolled for a long time you are likely to find scorched parts like this. Whereas a plane that runs its tanks try and crashes in a field may not see the same fire marks. However, if the plane hits the ground with enough force the heat generated from the impact can also lead to markings like this.
$endgroup$
add a comment |
$begingroup$
First off, the engine is running around 2000° F (NOT 2000° C/3632° F) only in a few places within it. The Turbine Inlet Temperature (TIT) can be that high but cools rapidly when the exhaust gases are rapidly expanded through the high and low pressure turbines to exit at approx 1000° F at the jet pipe (enthalpy is converted into mechanical work here). Most sections of the engine are not designed for that high of a temperature and may well oxidize or deform in the post crash fire.
UPDATE: While I do not have definitive values for the max TIT of a CFM-LEAP engine, a good estimate would be around 1500°- 1600° C (2732° - 2912° F) as this represents about the state of the art for gas turbines outside of a few military applications. This source quotes that the Pratt & Whitney F-135 can operate at TITs of 2000° C due to its use of a proprietary ceramic coating over single crystal nickel cobalt superalloys for the hot section. It is unclear whether that is a sustained engine power setting or simply a max operating temp prior to destruction. This is NOT representative of a typical aviation gas turbine, which run much cooler. I would stand by my original figure of 1000-1200° C TIT for earlier gas turbines eg PT-6, J85, J79, etc.
$endgroup$
3
$begingroup$
Note: 2000° F is 1093° C
$endgroup$
– Ring Ø
Mar 13 at 14:18
2
$begingroup$
@CarloFelicione probably to inform people like me what the celsius equivalent to 2000° F is (seeing as celsius is something you provide for the other value, and most of the world understands over fahrenheit)
$endgroup$
– CalvT
Mar 13 at 17:22
1
$begingroup$
This disagrees with the temperatures quoted in other answers.
$endgroup$
– Carl Witthoft
Mar 13 at 18:48
1
$begingroup$
This does disagree with the answer by Zach Lipton which quotes a source as stating "2000 Celcius" (and links the source).
$endgroup$
– Martin Bonner
Mar 13 at 21:10
2
$begingroup$
Do you have a citation for this figure? The Stanford link that Zach quoted above specifically states "up to 2000 degrees Celsius", and the chart posted by Dave appears to peak at around 1788 degrees Celsius (~3200 F).
$endgroup$
– GalacticCowboy
Mar 13 at 21:10
|
show 8 more comments
Your Answer
StackExchange.ifUsing("editor", function () {
return StackExchange.using("mathjaxEditing", function () {
StackExchange.MarkdownEditor.creationCallbacks.add(function (editor, postfix) {
StackExchange.mathjaxEditing.prepareWmdForMathJax(editor, postfix, [["$", "$"], ["\\(","\\)"]]);
});
});
}, "mathjax-editing");
StackExchange.ready(function() {
var channelOptions = {
tags: "".split(" "),
id: "528"
};
initTagRenderer("".split(" "), "".split(" "), channelOptions);
StackExchange.using("externalEditor", function() {
// Have to fire editor after snippets, if snippets enabled
if (StackExchange.settings.snippets.snippetsEnabled) {
StackExchange.using("snippets", function() {
createEditor();
});
}
else {
createEditor();
}
});
function createEditor() {
StackExchange.prepareEditor({
heartbeatType: 'answer',
autoActivateHeartbeat: false,
convertImagesToLinks: false,
noModals: true,
showLowRepImageUploadWarning: true,
reputationToPostImages: null,
bindNavPrevention: true,
postfix: "",
imageUploader: {
brandingHtml: "Powered by u003ca class="icon-imgur-white" href="https://imgur.com/"u003eu003c/au003e",
contentPolicyHtml: "User contributions licensed under u003ca href="https://creativecommons.org/licenses/by-sa/3.0/"u003ecc by-sa 3.0 with attribution requiredu003c/au003e u003ca href="https://stackoverflow.com/legal/content-policy"u003e(content policy)u003c/au003e",
allowUrls: true
},
noCode: true, onDemand: true,
discardSelector: ".discard-answer"
,immediatelyShowMarkdownHelp:true
});
}
});
Sign up or log in
StackExchange.ready(function () {
StackExchange.helpers.onClickDraftSave('#login-link');
});
Sign up using Google
Sign up using Facebook
Sign up using Email and Password
Post as a guest
Required, but never shown
StackExchange.ready(
function () {
StackExchange.openid.initPostLogin('.new-post-login', 'https%3a%2f%2faviation.stackexchange.com%2fquestions%2f61046%2fwhy-would-a-jet-engine-that-runs-at-temps-excess-of-2000c-burn-when-it-crashes%23new-answer', 'question_page');
}
);
Post as a guest
Required, but never shown
3 Answers
3
active
oldest
votes
3 Answers
3
active
oldest
votes
active
oldest
votes
active
oldest
votes
$begingroup$
How The Jet Engine Works:
Inside the typical commercial jet engine, the fuel burns in the combustion chamber at up to 2000 degrees Celsius. The temperature at which metals in this part of the engine start to melt is 1300 degrees Celsius, so advanced cooling techniques must be used.
You can read more about some of those cooling mechanisms in How are temperature differences handled in a jet engine?
See also, How do you stop a jet engine melting?:
Neil - The normal melting point of the nickel blade alloys that we use in the turbine is typically about 12-1400 degrees. But what you do, and this is the clever bit, is you actually cool these blades. You have internal cooling passages, which effectively has air that flows through and it's about 7-800 degrees. And this cooling air then exits from small little minute holes that have been drilled on the surface of the blade and this air then forms a kind of a film on the surface of the blade, and this technology is typically called a 'film cooling.'
What you also do - you coat these blades and typically use something called a thermal barrier coating. The thermal barrier coating, effectively, is ceramic, typically about quarter of a millimeter in thickness, but they have got very, very low thermal conductivity. So, effectively, even though the gas stream is at a much higher air temperature, the effective metal that exists beneath the thermal barrier coating is much colder, and you get thermal grade of the order of about 100 degrees C between the hot and the cold surface. So all of this put together - this whole cooling technology effectively helps to keep the blade below its melting temperature.
The engine is designed to manage the intense heat in a controlled way, by restricting it to certain components, injecting cool air around the hot parts, and choosing different materials for different parts of the engine. If the engine is severely damaged, doused in jet fuel, and set on fire, none of those mechanisms function; the entire engine (or whatever is left of it), as opposed to just the portions intended to manage heat, will be hot, and none of the cooling mechanisms will be working.
$endgroup$
$begingroup$
Those blades are little marvels of engineering. Something you can hold in one hand but costs some ~5000 dollars (and there's a whole lot of them in one turbine)
$endgroup$
– mbrig
Mar 13 at 2:37
2
$begingroup$
@Dannie Yes, turbine blades can be handled with your bare hands and used. The metals are nickle based super alloys and they sometime have a ceramic thermal barrier coating they are very environmentally stable. When assembling an engine, they actually use beeswax to hold seals in place and it just burns off once the engine is ran.
$endgroup$
– OSUZorba
Mar 14 at 4:13
1
$begingroup$
I'd like to add, that although the superalloys can make it to ~1400C before they melt, they will oxidize ("burn") at lower temperatures. The picture to me looks mostly like impact damage to me with some oxidization. Part of the reason it looks like impact damage to me is that materials with low melting/oxidation points are still there, but then materials with very high melting points are not.
$endgroup$
– OSUZorba
Mar 14 at 4:30
2
$begingroup$
So you're telling me that a jet engine actually operates above the melting point of the turbine blades? And that they are kept solid by some sophisticated aerodynamics? And if that fails, the entire engine will presumably turn into a blob of lava? I wish I hadn't read that now...
$endgroup$
– Oscar Bravo
Mar 14 at 7:35
1
$begingroup$
@OSUZorba it's even cleverer than that. The surface isn't the same as the bulk, but a thin layer of nickel aluminide (some blades anyway) with a high thermal conductivity and high melting point (~1600-1900C). This reacts in service to form Al2O3 (sapphire), MP ~2000C, but if blades are overhauled the sapphire must be removed before recoating. Paper from some former colleagues of mine. I've handled the blades in question, which I believe were miltary.
$endgroup$
– Chris H
Mar 14 at 9:23
|
show 4 more comments
$begingroup$
How The Jet Engine Works:
Inside the typical commercial jet engine, the fuel burns in the combustion chamber at up to 2000 degrees Celsius. The temperature at which metals in this part of the engine start to melt is 1300 degrees Celsius, so advanced cooling techniques must be used.
You can read more about some of those cooling mechanisms in How are temperature differences handled in a jet engine?
See also, How do you stop a jet engine melting?:
Neil - The normal melting point of the nickel blade alloys that we use in the turbine is typically about 12-1400 degrees. But what you do, and this is the clever bit, is you actually cool these blades. You have internal cooling passages, which effectively has air that flows through and it's about 7-800 degrees. And this cooling air then exits from small little minute holes that have been drilled on the surface of the blade and this air then forms a kind of a film on the surface of the blade, and this technology is typically called a 'film cooling.'
What you also do - you coat these blades and typically use something called a thermal barrier coating. The thermal barrier coating, effectively, is ceramic, typically about quarter of a millimeter in thickness, but they have got very, very low thermal conductivity. So, effectively, even though the gas stream is at a much higher air temperature, the effective metal that exists beneath the thermal barrier coating is much colder, and you get thermal grade of the order of about 100 degrees C between the hot and the cold surface. So all of this put together - this whole cooling technology effectively helps to keep the blade below its melting temperature.
The engine is designed to manage the intense heat in a controlled way, by restricting it to certain components, injecting cool air around the hot parts, and choosing different materials for different parts of the engine. If the engine is severely damaged, doused in jet fuel, and set on fire, none of those mechanisms function; the entire engine (or whatever is left of it), as opposed to just the portions intended to manage heat, will be hot, and none of the cooling mechanisms will be working.
$endgroup$
$begingroup$
Those blades are little marvels of engineering. Something you can hold in one hand but costs some ~5000 dollars (and there's a whole lot of them in one turbine)
$endgroup$
– mbrig
Mar 13 at 2:37
2
$begingroup$
@Dannie Yes, turbine blades can be handled with your bare hands and used. The metals are nickle based super alloys and they sometime have a ceramic thermal barrier coating they are very environmentally stable. When assembling an engine, they actually use beeswax to hold seals in place and it just burns off once the engine is ran.
$endgroup$
– OSUZorba
Mar 14 at 4:13
1
$begingroup$
I'd like to add, that although the superalloys can make it to ~1400C before they melt, they will oxidize ("burn") at lower temperatures. The picture to me looks mostly like impact damage to me with some oxidization. Part of the reason it looks like impact damage to me is that materials with low melting/oxidation points are still there, but then materials with very high melting points are not.
$endgroup$
– OSUZorba
Mar 14 at 4:30
2
$begingroup$
So you're telling me that a jet engine actually operates above the melting point of the turbine blades? And that they are kept solid by some sophisticated aerodynamics? And if that fails, the entire engine will presumably turn into a blob of lava? I wish I hadn't read that now...
$endgroup$
– Oscar Bravo
Mar 14 at 7:35
1
$begingroup$
@OSUZorba it's even cleverer than that. The surface isn't the same as the bulk, but a thin layer of nickel aluminide (some blades anyway) with a high thermal conductivity and high melting point (~1600-1900C). This reacts in service to form Al2O3 (sapphire), MP ~2000C, but if blades are overhauled the sapphire must be removed before recoating. Paper from some former colleagues of mine. I've handled the blades in question, which I believe were miltary.
$endgroup$
– Chris H
Mar 14 at 9:23
|
show 4 more comments
$begingroup$
How The Jet Engine Works:
Inside the typical commercial jet engine, the fuel burns in the combustion chamber at up to 2000 degrees Celsius. The temperature at which metals in this part of the engine start to melt is 1300 degrees Celsius, so advanced cooling techniques must be used.
You can read more about some of those cooling mechanisms in How are temperature differences handled in a jet engine?
See also, How do you stop a jet engine melting?:
Neil - The normal melting point of the nickel blade alloys that we use in the turbine is typically about 12-1400 degrees. But what you do, and this is the clever bit, is you actually cool these blades. You have internal cooling passages, which effectively has air that flows through and it's about 7-800 degrees. And this cooling air then exits from small little minute holes that have been drilled on the surface of the blade and this air then forms a kind of a film on the surface of the blade, and this technology is typically called a 'film cooling.'
What you also do - you coat these blades and typically use something called a thermal barrier coating. The thermal barrier coating, effectively, is ceramic, typically about quarter of a millimeter in thickness, but they have got very, very low thermal conductivity. So, effectively, even though the gas stream is at a much higher air temperature, the effective metal that exists beneath the thermal barrier coating is much colder, and you get thermal grade of the order of about 100 degrees C between the hot and the cold surface. So all of this put together - this whole cooling technology effectively helps to keep the blade below its melting temperature.
The engine is designed to manage the intense heat in a controlled way, by restricting it to certain components, injecting cool air around the hot parts, and choosing different materials for different parts of the engine. If the engine is severely damaged, doused in jet fuel, and set on fire, none of those mechanisms function; the entire engine (or whatever is left of it), as opposed to just the portions intended to manage heat, will be hot, and none of the cooling mechanisms will be working.
$endgroup$
How The Jet Engine Works:
Inside the typical commercial jet engine, the fuel burns in the combustion chamber at up to 2000 degrees Celsius. The temperature at which metals in this part of the engine start to melt is 1300 degrees Celsius, so advanced cooling techniques must be used.
You can read more about some of those cooling mechanisms in How are temperature differences handled in a jet engine?
See also, How do you stop a jet engine melting?:
Neil - The normal melting point of the nickel blade alloys that we use in the turbine is typically about 12-1400 degrees. But what you do, and this is the clever bit, is you actually cool these blades. You have internal cooling passages, which effectively has air that flows through and it's about 7-800 degrees. And this cooling air then exits from small little minute holes that have been drilled on the surface of the blade and this air then forms a kind of a film on the surface of the blade, and this technology is typically called a 'film cooling.'
What you also do - you coat these blades and typically use something called a thermal barrier coating. The thermal barrier coating, effectively, is ceramic, typically about quarter of a millimeter in thickness, but they have got very, very low thermal conductivity. So, effectively, even though the gas stream is at a much higher air temperature, the effective metal that exists beneath the thermal barrier coating is much colder, and you get thermal grade of the order of about 100 degrees C between the hot and the cold surface. So all of this put together - this whole cooling technology effectively helps to keep the blade below its melting temperature.
The engine is designed to manage the intense heat in a controlled way, by restricting it to certain components, injecting cool air around the hot parts, and choosing different materials for different parts of the engine. If the engine is severely damaged, doused in jet fuel, and set on fire, none of those mechanisms function; the entire engine (or whatever is left of it), as opposed to just the portions intended to manage heat, will be hot, and none of the cooling mechanisms will be working.
edited Mar 12 at 22:53
answered Mar 12 at 22:49
Zach LiptonZach Lipton
6,46412642
6,46412642
$begingroup$
Those blades are little marvels of engineering. Something you can hold in one hand but costs some ~5000 dollars (and there's a whole lot of them in one turbine)
$endgroup$
– mbrig
Mar 13 at 2:37
2
$begingroup$
@Dannie Yes, turbine blades can be handled with your bare hands and used. The metals are nickle based super alloys and they sometime have a ceramic thermal barrier coating they are very environmentally stable. When assembling an engine, they actually use beeswax to hold seals in place and it just burns off once the engine is ran.
$endgroup$
– OSUZorba
Mar 14 at 4:13
1
$begingroup$
I'd like to add, that although the superalloys can make it to ~1400C before they melt, they will oxidize ("burn") at lower temperatures. The picture to me looks mostly like impact damage to me with some oxidization. Part of the reason it looks like impact damage to me is that materials with low melting/oxidation points are still there, but then materials with very high melting points are not.
$endgroup$
– OSUZorba
Mar 14 at 4:30
2
$begingroup$
So you're telling me that a jet engine actually operates above the melting point of the turbine blades? And that they are kept solid by some sophisticated aerodynamics? And if that fails, the entire engine will presumably turn into a blob of lava? I wish I hadn't read that now...
$endgroup$
– Oscar Bravo
Mar 14 at 7:35
1
$begingroup$
@OSUZorba it's even cleverer than that. The surface isn't the same as the bulk, but a thin layer of nickel aluminide (some blades anyway) with a high thermal conductivity and high melting point (~1600-1900C). This reacts in service to form Al2O3 (sapphire), MP ~2000C, but if blades are overhauled the sapphire must be removed before recoating. Paper from some former colleagues of mine. I've handled the blades in question, which I believe were miltary.
$endgroup$
– Chris H
Mar 14 at 9:23
|
show 4 more comments
$begingroup$
Those blades are little marvels of engineering. Something you can hold in one hand but costs some ~5000 dollars (and there's a whole lot of them in one turbine)
$endgroup$
– mbrig
Mar 13 at 2:37
2
$begingroup$
@Dannie Yes, turbine blades can be handled with your bare hands and used. The metals are nickle based super alloys and they sometime have a ceramic thermal barrier coating they are very environmentally stable. When assembling an engine, they actually use beeswax to hold seals in place and it just burns off once the engine is ran.
$endgroup$
– OSUZorba
Mar 14 at 4:13
1
$begingroup$
I'd like to add, that although the superalloys can make it to ~1400C before they melt, they will oxidize ("burn") at lower temperatures. The picture to me looks mostly like impact damage to me with some oxidization. Part of the reason it looks like impact damage to me is that materials with low melting/oxidation points are still there, but then materials with very high melting points are not.
$endgroup$
– OSUZorba
Mar 14 at 4:30
2
$begingroup$
So you're telling me that a jet engine actually operates above the melting point of the turbine blades? And that they are kept solid by some sophisticated aerodynamics? And if that fails, the entire engine will presumably turn into a blob of lava? I wish I hadn't read that now...
$endgroup$
– Oscar Bravo
Mar 14 at 7:35
1
$begingroup$
@OSUZorba it's even cleverer than that. The surface isn't the same as the bulk, but a thin layer of nickel aluminide (some blades anyway) with a high thermal conductivity and high melting point (~1600-1900C). This reacts in service to form Al2O3 (sapphire), MP ~2000C, but if blades are overhauled the sapphire must be removed before recoating. Paper from some former colleagues of mine. I've handled the blades in question, which I believe were miltary.
$endgroup$
– Chris H
Mar 14 at 9:23
$begingroup$
Those blades are little marvels of engineering. Something you can hold in one hand but costs some ~5000 dollars (and there's a whole lot of them in one turbine)
$endgroup$
– mbrig
Mar 13 at 2:37
$begingroup$
Those blades are little marvels of engineering. Something you can hold in one hand but costs some ~5000 dollars (and there's a whole lot of them in one turbine)
$endgroup$
– mbrig
Mar 13 at 2:37
2
2
$begingroup$
@Dannie Yes, turbine blades can be handled with your bare hands and used. The metals are nickle based super alloys and they sometime have a ceramic thermal barrier coating they are very environmentally stable. When assembling an engine, they actually use beeswax to hold seals in place and it just burns off once the engine is ran.
$endgroup$
– OSUZorba
Mar 14 at 4:13
$begingroup$
@Dannie Yes, turbine blades can be handled with your bare hands and used. The metals are nickle based super alloys and they sometime have a ceramic thermal barrier coating they are very environmentally stable. When assembling an engine, they actually use beeswax to hold seals in place and it just burns off once the engine is ran.
$endgroup$
– OSUZorba
Mar 14 at 4:13
1
1
$begingroup$
I'd like to add, that although the superalloys can make it to ~1400C before they melt, they will oxidize ("burn") at lower temperatures. The picture to me looks mostly like impact damage to me with some oxidization. Part of the reason it looks like impact damage to me is that materials with low melting/oxidation points are still there, but then materials with very high melting points are not.
$endgroup$
– OSUZorba
Mar 14 at 4:30
$begingroup$
I'd like to add, that although the superalloys can make it to ~1400C before they melt, they will oxidize ("burn") at lower temperatures. The picture to me looks mostly like impact damage to me with some oxidization. Part of the reason it looks like impact damage to me is that materials with low melting/oxidation points are still there, but then materials with very high melting points are not.
$endgroup$
– OSUZorba
Mar 14 at 4:30
2
2
$begingroup$
So you're telling me that a jet engine actually operates above the melting point of the turbine blades? And that they are kept solid by some sophisticated aerodynamics? And if that fails, the entire engine will presumably turn into a blob of lava? I wish I hadn't read that now...
$endgroup$
– Oscar Bravo
Mar 14 at 7:35
$begingroup$
So you're telling me that a jet engine actually operates above the melting point of the turbine blades? And that they are kept solid by some sophisticated aerodynamics? And if that fails, the entire engine will presumably turn into a blob of lava? I wish I hadn't read that now...
$endgroup$
– Oscar Bravo
Mar 14 at 7:35
1
1
$begingroup$
@OSUZorba it's even cleverer than that. The surface isn't the same as the bulk, but a thin layer of nickel aluminide (some blades anyway) with a high thermal conductivity and high melting point (~1600-1900C). This reacts in service to form Al2O3 (sapphire), MP ~2000C, but if blades are overhauled the sapphire must be removed before recoating. Paper from some former colleagues of mine. I've handled the blades in question, which I believe were miltary.
$endgroup$
– Chris H
Mar 14 at 9:23
$begingroup$
@OSUZorba it's even cleverer than that. The surface isn't the same as the bulk, but a thin layer of nickel aluminide (some blades anyway) with a high thermal conductivity and high melting point (~1600-1900C). This reacts in service to form Al2O3 (sapphire), MP ~2000C, but if blades are overhauled the sapphire must be removed before recoating. Paper from some former colleagues of mine. I've handled the blades in question, which I believe were miltary.
$endgroup$
– Chris H
Mar 14 at 9:23
|
show 4 more comments
$begingroup$
Peter's answer to another question has a nice chart that shows internal jet engine temperatures:
You can see that the temperatures are highest by a fairly large factor in the combustion chamber. This means that only the combustion chamber needs to be able to withstand those temperatures. To save weight and often use less expensive and less exotic materials, the rest of the engine may be made out of materials that don't need to withstand such high temperatures. As such, in an accident where jet fuel may be dispersed in an uncontrolled way and burn with as much oxygen as it can get, it's easy to scorch engine parts and anything else around.
It also is in part a question of time. The ability to withstand heat varies with time. In a crash of a fairly fueled aircraft that may burn uncontrolled for a long time you are likely to find scorched parts like this. Whereas a plane that runs its tanks try and crashes in a field may not see the same fire marks. However, if the plane hits the ground with enough force the heat generated from the impact can also lead to markings like this.
$endgroup$
add a comment |
$begingroup$
Peter's answer to another question has a nice chart that shows internal jet engine temperatures:
You can see that the temperatures are highest by a fairly large factor in the combustion chamber. This means that only the combustion chamber needs to be able to withstand those temperatures. To save weight and often use less expensive and less exotic materials, the rest of the engine may be made out of materials that don't need to withstand such high temperatures. As such, in an accident where jet fuel may be dispersed in an uncontrolled way and burn with as much oxygen as it can get, it's easy to scorch engine parts and anything else around.
It also is in part a question of time. The ability to withstand heat varies with time. In a crash of a fairly fueled aircraft that may burn uncontrolled for a long time you are likely to find scorched parts like this. Whereas a plane that runs its tanks try and crashes in a field may not see the same fire marks. However, if the plane hits the ground with enough force the heat generated from the impact can also lead to markings like this.
$endgroup$
add a comment |
$begingroup$
Peter's answer to another question has a nice chart that shows internal jet engine temperatures:
You can see that the temperatures are highest by a fairly large factor in the combustion chamber. This means that only the combustion chamber needs to be able to withstand those temperatures. To save weight and often use less expensive and less exotic materials, the rest of the engine may be made out of materials that don't need to withstand such high temperatures. As such, in an accident where jet fuel may be dispersed in an uncontrolled way and burn with as much oxygen as it can get, it's easy to scorch engine parts and anything else around.
It also is in part a question of time. The ability to withstand heat varies with time. In a crash of a fairly fueled aircraft that may burn uncontrolled for a long time you are likely to find scorched parts like this. Whereas a plane that runs its tanks try and crashes in a field may not see the same fire marks. However, if the plane hits the ground with enough force the heat generated from the impact can also lead to markings like this.
$endgroup$
Peter's answer to another question has a nice chart that shows internal jet engine temperatures:
You can see that the temperatures are highest by a fairly large factor in the combustion chamber. This means that only the combustion chamber needs to be able to withstand those temperatures. To save weight and often use less expensive and less exotic materials, the rest of the engine may be made out of materials that don't need to withstand such high temperatures. As such, in an accident where jet fuel may be dispersed in an uncontrolled way and burn with as much oxygen as it can get, it's easy to scorch engine parts and anything else around.
It also is in part a question of time. The ability to withstand heat varies with time. In a crash of a fairly fueled aircraft that may burn uncontrolled for a long time you are likely to find scorched parts like this. Whereas a plane that runs its tanks try and crashes in a field may not see the same fire marks. However, if the plane hits the ground with enough force the heat generated from the impact can also lead to markings like this.
edited Mar 13 at 11:08
Peter Mortensen
30727
30727
answered Mar 12 at 22:41
DaveDave
67.5k4127243
67.5k4127243
add a comment |
add a comment |
$begingroup$
First off, the engine is running around 2000° F (NOT 2000° C/3632° F) only in a few places within it. The Turbine Inlet Temperature (TIT) can be that high but cools rapidly when the exhaust gases are rapidly expanded through the high and low pressure turbines to exit at approx 1000° F at the jet pipe (enthalpy is converted into mechanical work here). Most sections of the engine are not designed for that high of a temperature and may well oxidize or deform in the post crash fire.
UPDATE: While I do not have definitive values for the max TIT of a CFM-LEAP engine, a good estimate would be around 1500°- 1600° C (2732° - 2912° F) as this represents about the state of the art for gas turbines outside of a few military applications. This source quotes that the Pratt & Whitney F-135 can operate at TITs of 2000° C due to its use of a proprietary ceramic coating over single crystal nickel cobalt superalloys for the hot section. It is unclear whether that is a sustained engine power setting or simply a max operating temp prior to destruction. This is NOT representative of a typical aviation gas turbine, which run much cooler. I would stand by my original figure of 1000-1200° C TIT for earlier gas turbines eg PT-6, J85, J79, etc.
$endgroup$
3
$begingroup$
Note: 2000° F is 1093° C
$endgroup$
– Ring Ø
Mar 13 at 14:18
2
$begingroup$
@CarloFelicione probably to inform people like me what the celsius equivalent to 2000° F is (seeing as celsius is something you provide for the other value, and most of the world understands over fahrenheit)
$endgroup$
– CalvT
Mar 13 at 17:22
1
$begingroup$
This disagrees with the temperatures quoted in other answers.
$endgroup$
– Carl Witthoft
Mar 13 at 18:48
1
$begingroup$
This does disagree with the answer by Zach Lipton which quotes a source as stating "2000 Celcius" (and links the source).
$endgroup$
– Martin Bonner
Mar 13 at 21:10
2
$begingroup$
Do you have a citation for this figure? The Stanford link that Zach quoted above specifically states "up to 2000 degrees Celsius", and the chart posted by Dave appears to peak at around 1788 degrees Celsius (~3200 F).
$endgroup$
– GalacticCowboy
Mar 13 at 21:10
|
show 8 more comments
$begingroup$
First off, the engine is running around 2000° F (NOT 2000° C/3632° F) only in a few places within it. The Turbine Inlet Temperature (TIT) can be that high but cools rapidly when the exhaust gases are rapidly expanded through the high and low pressure turbines to exit at approx 1000° F at the jet pipe (enthalpy is converted into mechanical work here). Most sections of the engine are not designed for that high of a temperature and may well oxidize or deform in the post crash fire.
UPDATE: While I do not have definitive values for the max TIT of a CFM-LEAP engine, a good estimate would be around 1500°- 1600° C (2732° - 2912° F) as this represents about the state of the art for gas turbines outside of a few military applications. This source quotes that the Pratt & Whitney F-135 can operate at TITs of 2000° C due to its use of a proprietary ceramic coating over single crystal nickel cobalt superalloys for the hot section. It is unclear whether that is a sustained engine power setting or simply a max operating temp prior to destruction. This is NOT representative of a typical aviation gas turbine, which run much cooler. I would stand by my original figure of 1000-1200° C TIT for earlier gas turbines eg PT-6, J85, J79, etc.
$endgroup$
3
$begingroup$
Note: 2000° F is 1093° C
$endgroup$
– Ring Ø
Mar 13 at 14:18
2
$begingroup$
@CarloFelicione probably to inform people like me what the celsius equivalent to 2000° F is (seeing as celsius is something you provide for the other value, and most of the world understands over fahrenheit)
$endgroup$
– CalvT
Mar 13 at 17:22
1
$begingroup$
This disagrees with the temperatures quoted in other answers.
$endgroup$
– Carl Witthoft
Mar 13 at 18:48
1
$begingroup$
This does disagree with the answer by Zach Lipton which quotes a source as stating "2000 Celcius" (and links the source).
$endgroup$
– Martin Bonner
Mar 13 at 21:10
2
$begingroup$
Do you have a citation for this figure? The Stanford link that Zach quoted above specifically states "up to 2000 degrees Celsius", and the chart posted by Dave appears to peak at around 1788 degrees Celsius (~3200 F).
$endgroup$
– GalacticCowboy
Mar 13 at 21:10
|
show 8 more comments
$begingroup$
First off, the engine is running around 2000° F (NOT 2000° C/3632° F) only in a few places within it. The Turbine Inlet Temperature (TIT) can be that high but cools rapidly when the exhaust gases are rapidly expanded through the high and low pressure turbines to exit at approx 1000° F at the jet pipe (enthalpy is converted into mechanical work here). Most sections of the engine are not designed for that high of a temperature and may well oxidize or deform in the post crash fire.
UPDATE: While I do not have definitive values for the max TIT of a CFM-LEAP engine, a good estimate would be around 1500°- 1600° C (2732° - 2912° F) as this represents about the state of the art for gas turbines outside of a few military applications. This source quotes that the Pratt & Whitney F-135 can operate at TITs of 2000° C due to its use of a proprietary ceramic coating over single crystal nickel cobalt superalloys for the hot section. It is unclear whether that is a sustained engine power setting or simply a max operating temp prior to destruction. This is NOT representative of a typical aviation gas turbine, which run much cooler. I would stand by my original figure of 1000-1200° C TIT for earlier gas turbines eg PT-6, J85, J79, etc.
$endgroup$
First off, the engine is running around 2000° F (NOT 2000° C/3632° F) only in a few places within it. The Turbine Inlet Temperature (TIT) can be that high but cools rapidly when the exhaust gases are rapidly expanded through the high and low pressure turbines to exit at approx 1000° F at the jet pipe (enthalpy is converted into mechanical work here). Most sections of the engine are not designed for that high of a temperature and may well oxidize or deform in the post crash fire.
UPDATE: While I do not have definitive values for the max TIT of a CFM-LEAP engine, a good estimate would be around 1500°- 1600° C (2732° - 2912° F) as this represents about the state of the art for gas turbines outside of a few military applications. This source quotes that the Pratt & Whitney F-135 can operate at TITs of 2000° C due to its use of a proprietary ceramic coating over single crystal nickel cobalt superalloys for the hot section. It is unclear whether that is a sustained engine power setting or simply a max operating temp prior to destruction. This is NOT representative of a typical aviation gas turbine, which run much cooler. I would stand by my original figure of 1000-1200° C TIT for earlier gas turbines eg PT-6, J85, J79, etc.
edited Mar 13 at 22:54
answered Mar 13 at 12:15


Carlo FelicioneCarlo Felicione
42.9k478155
42.9k478155
3
$begingroup$
Note: 2000° F is 1093° C
$endgroup$
– Ring Ø
Mar 13 at 14:18
2
$begingroup$
@CarloFelicione probably to inform people like me what the celsius equivalent to 2000° F is (seeing as celsius is something you provide for the other value, and most of the world understands over fahrenheit)
$endgroup$
– CalvT
Mar 13 at 17:22
1
$begingroup$
This disagrees with the temperatures quoted in other answers.
$endgroup$
– Carl Witthoft
Mar 13 at 18:48
1
$begingroup$
This does disagree with the answer by Zach Lipton which quotes a source as stating "2000 Celcius" (and links the source).
$endgroup$
– Martin Bonner
Mar 13 at 21:10
2
$begingroup$
Do you have a citation for this figure? The Stanford link that Zach quoted above specifically states "up to 2000 degrees Celsius", and the chart posted by Dave appears to peak at around 1788 degrees Celsius (~3200 F).
$endgroup$
– GalacticCowboy
Mar 13 at 21:10
|
show 8 more comments
3
$begingroup$
Note: 2000° F is 1093° C
$endgroup$
– Ring Ø
Mar 13 at 14:18
2
$begingroup$
@CarloFelicione probably to inform people like me what the celsius equivalent to 2000° F is (seeing as celsius is something you provide for the other value, and most of the world understands over fahrenheit)
$endgroup$
– CalvT
Mar 13 at 17:22
1
$begingroup$
This disagrees with the temperatures quoted in other answers.
$endgroup$
– Carl Witthoft
Mar 13 at 18:48
1
$begingroup$
This does disagree with the answer by Zach Lipton which quotes a source as stating "2000 Celcius" (and links the source).
$endgroup$
– Martin Bonner
Mar 13 at 21:10
2
$begingroup$
Do you have a citation for this figure? The Stanford link that Zach quoted above specifically states "up to 2000 degrees Celsius", and the chart posted by Dave appears to peak at around 1788 degrees Celsius (~3200 F).
$endgroup$
– GalacticCowboy
Mar 13 at 21:10
3
3
$begingroup$
Note: 2000° F is 1093° C
$endgroup$
– Ring Ø
Mar 13 at 14:18
$begingroup$
Note: 2000° F is 1093° C
$endgroup$
– Ring Ø
Mar 13 at 14:18
2
2
$begingroup$
@CarloFelicione probably to inform people like me what the celsius equivalent to 2000° F is (seeing as celsius is something you provide for the other value, and most of the world understands over fahrenheit)
$endgroup$
– CalvT
Mar 13 at 17:22
$begingroup$
@CarloFelicione probably to inform people like me what the celsius equivalent to 2000° F is (seeing as celsius is something you provide for the other value, and most of the world understands over fahrenheit)
$endgroup$
– CalvT
Mar 13 at 17:22
1
1
$begingroup$
This disagrees with the temperatures quoted in other answers.
$endgroup$
– Carl Witthoft
Mar 13 at 18:48
$begingroup$
This disagrees with the temperatures quoted in other answers.
$endgroup$
– Carl Witthoft
Mar 13 at 18:48
1
1
$begingroup$
This does disagree with the answer by Zach Lipton which quotes a source as stating "2000 Celcius" (and links the source).
$endgroup$
– Martin Bonner
Mar 13 at 21:10
$begingroup$
This does disagree with the answer by Zach Lipton which quotes a source as stating "2000 Celcius" (and links the source).
$endgroup$
– Martin Bonner
Mar 13 at 21:10
2
2
$begingroup$
Do you have a citation for this figure? The Stanford link that Zach quoted above specifically states "up to 2000 degrees Celsius", and the chart posted by Dave appears to peak at around 1788 degrees Celsius (~3200 F).
$endgroup$
– GalacticCowboy
Mar 13 at 21:10
$begingroup$
Do you have a citation for this figure? The Stanford link that Zach quoted above specifically states "up to 2000 degrees Celsius", and the chart posted by Dave appears to peak at around 1788 degrees Celsius (~3200 F).
$endgroup$
– GalacticCowboy
Mar 13 at 21:10
|
show 8 more comments
Thanks for contributing an answer to Aviation Stack Exchange!
- Please be sure to answer the question. Provide details and share your research!
But avoid …
- Asking for help, clarification, or responding to other answers.
- Making statements based on opinion; back them up with references or personal experience.
Use MathJax to format equations. MathJax reference.
To learn more, see our tips on writing great answers.
Sign up or log in
StackExchange.ready(function () {
StackExchange.helpers.onClickDraftSave('#login-link');
});
Sign up using Google
Sign up using Facebook
Sign up using Email and Password
Post as a guest
Required, but never shown
StackExchange.ready(
function () {
StackExchange.openid.initPostLogin('.new-post-login', 'https%3a%2f%2faviation.stackexchange.com%2fquestions%2f61046%2fwhy-would-a-jet-engine-that-runs-at-temps-excess-of-2000c-burn-when-it-crashes%23new-answer', 'question_page');
}
);
Post as a guest
Required, but never shown
Sign up or log in
StackExchange.ready(function () {
StackExchange.helpers.onClickDraftSave('#login-link');
});
Sign up using Google
Sign up using Facebook
Sign up using Email and Password
Post as a guest
Required, but never shown
Sign up or log in
StackExchange.ready(function () {
StackExchange.helpers.onClickDraftSave('#login-link');
});
Sign up using Google
Sign up using Facebook
Sign up using Email and Password
Post as a guest
Required, but never shown
Sign up or log in
StackExchange.ready(function () {
StackExchange.helpers.onClickDraftSave('#login-link');
});
Sign up using Google
Sign up using Facebook
Sign up using Email and Password
Sign up using Google
Sign up using Facebook
Sign up using Email and Password
Post as a guest
Required, but never shown
Required, but never shown
Required, but never shown
Required, but never shown
Required, but never shown
Required, but never shown
Required, but never shown
Required, but never shown
Required, but never shown
e7eP RuQNMOCNpFT77hGQw4vHLP4Q,c EMf OrD mgNgTHE,F,0mZNMCykd,rM2KMpe3pu37C2agZDv6RLIhNOwhxXp,7oYFgyJuphoE aG
9
$begingroup$
The engine in the photograph is not melted.
$endgroup$
– Michael Hall
Mar 12 at 23:10
2
$begingroup$
@MichaelHall: That's on me, I've fixed it. OP originally wrote burnt. Although judging by the LP section, it did melt.
$endgroup$
– ymb1
Mar 12 at 23:36
21
$begingroup$
I have to challenge the premise. From the picture, it looks like the external housing of the engine burned and/or melted. The internal parts look like they've just suffered impact damage. The external housing does not experience high temperatures. Same reason the combustion temperature of your car's engine may reach 2000 C or so, yet the plastic components sitting nearby don't melt.
$endgroup$
– jamesqf
Mar 13 at 4:25
$begingroup$
related: aviation.stackexchange.com/a/16842/1467
$endgroup$
– Federico♦
Mar 13 at 9:11
2
$begingroup$
I think that the only thing we can say about the external housing is that it is missing from the picture. Besides melting or burning away it could have broken up on impact and pieces shed away as the core slid along the ground. Tough to surmise what happened from a single still photo.
$endgroup$
– Michael Hall
Mar 13 at 16:54